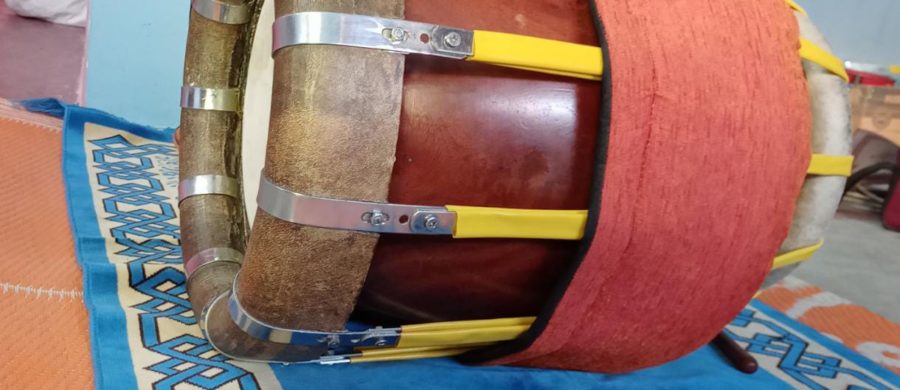
Panruti Kattai: Crafting Taste and Sound
Technology’s Stories vol. 9, no. 1 DOI: https://doi.org/10.15763/jou.ts.2021.03.23.03
Today, artisans in the Panruti region of South India are known for their construction of musical instruments, especially, the thavil, a double-headed drum, played by striking one head using a hand and the other with a stick. (See figure 1.) It is played for festivals, weddings, and other ceremonies. Normally, artisanal knowledge in India such as that required to make a thavil is understood to be held mainly within the caste and ethnic communities. This story moves beyond the boundaries of these communities to show the broader network involved in establishing and making viable both an instrument with a unique sound and a thriving craft community. To be sure this story explores the artisans who make these instruments. But by investigating how the craft spread to the Panruti region, it highlights how the growth of the community of artisans and the skills of instrument making was connected to local plantation-grown jackfruit trees, the climate and geography of Panruti, and the musicians who informed the instrument design. Therefore the history of instrument making in Panruti shows how both artisanal communities and wider networks of people and plants shape the instruments and the unique sound they produce.
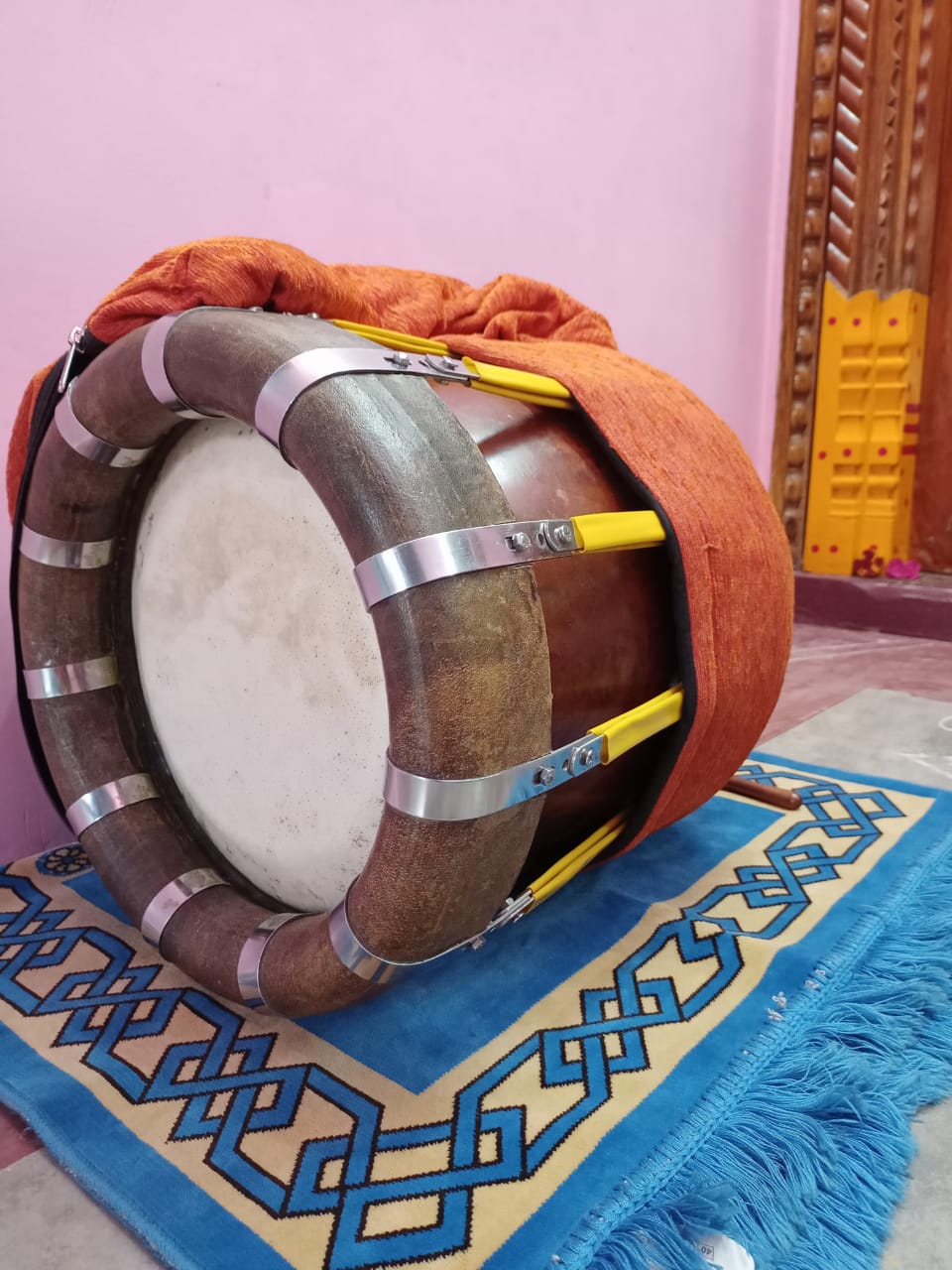
Figure 1: A thavil drum. Credit: Photo by Raju
The Move to Panruti
The craft of thavil-making in the nineteenth-century centered on the city of Tanjore (now Thanjavur) in Tamil Nadu. Panruti, located some 75 miles north of Tanjore emerged as a center of musical instrument making only in the middle of the twentieth century. At that time, one craftsman Somu Aasari moved to Panruti, possibly to take advantage of the jackfruit trees of the region. In the years since, the wood of the jackfruit tree has become the primary material to make musical instruments like the thavil, the mridangam, the pampai, and the veena.[1]
Sources are unclear as to exactly what motivated this move, but we can speculate that the resource crisis in the years just after World War II played a role. Woods traditionally used to make musical instruments like rosewood, sandalwood, mango, nana, margosa, and babool had become scarce.[2] Vernacular magazines on industry and trade published at the time back up this interpretation as they wrote extensively on the effects of war and the resource crisis on craft industries, especially in the Madras presidency.[3] Moreover, the scarcity of wood in the Tanjore region by this time required the expensive transportation of wood from regions like Panruti where wood was more plentiful. Therefore the availability of jackfruit wood in the region seems to have been one factor that stimulated the migration of craftspeople.[4] All the craftspeople who make musical instruments in Panruti today are connected with Somu Asarai. They either apprenticed with him or one of his students.[5]
Instrument-making did not figure at all in Panruti’s past before the arrival of Somu Asari. Colonial and vernacular documents show that Panruti’s fame came from its role as a hub for trade; located close to a port, it was well connected to two important colonial towns: British Madras and French Pondicherry, as well as to Burma. The economy of Panruti involved the sale of ground-nuts, clay toys, timber, much of which was used in the nearby shipbuilding yard in Cuddalore, and jackfruit which was brought from nearby forest and hill areas. The jackfruit trees of the region were known for their unusually large size.[6]
Colonial industrial surveys cite musical instrument making as an unprofitable craft.[7] It was not taught in the colonial industrial arts schools or the post-independent technical institutes of the country. There were no state efforts to move or start up new centers of musical instrument making. Instead, as music patronage slowly moved away from the royal court of Tanjore, musicians started traveling to towns for performances. Instrument makers were motivated to move their manufacture to places where they could be in ready contact with the musicians who needed their instruments. Thus Panruti’s resources and its history as a center of trade played a role in its ultimate transformation into a home for this community of musical-instrument craftspeople.
Crafting Sound Part 1: Jackfruit Trees and Craftspeople
Craft workers spend years learning how to choose the right wood for crafting a thavil drum as part of their apprenticeship. Yet the material they choose from has already been shaped by the work of plantation owners and workers who raise jackfruit trees. They plant local varieties of jackfruit which have been selected not for the yield of fruit but instead for premium timber. Indeed, cultivators consider jackfruit tree gold because they can earn a lump sum of money immediately by selling a tree due to the high demand in the region. During the cultivation process, planters harvest jackfruit early both to produce the sweetest fruits and to maintain the strength of the wood. Controlled irrigation likewise maintains the quality of the wood. A musical instrument maker will not buy a tree if it grows close to a watery area because too much water will weaken the wood.
Procuring local wood is challenging since the supply of wood is limited. Instrument-makers may thus compete for the best quality wood. Cultivators will not cut down a tree until an emergency or unforeseen situation arises. Craftspeople do not buy wood from agents or on the market. Instead, they work directly with the plantation owner. The instrument maker visits the plantation and inspects the jackfruit tree up for sale before finalizing the price. Once the tree is purchased, a craftworker will wait until the tree sheds its leaves before commissioning woodcutters to cut it down. Once the tree is cut down, the logs are kept in an open area to season until the wood is sufficiently dry. (See figure 2.) [8] The woodcutter cuts the tree into pieces, marked by the instrument maker to ensure that the pieces are of sufficient length to be usable.(See figure 3.) If the length falls short, they cannot use the wood for any other purpose.
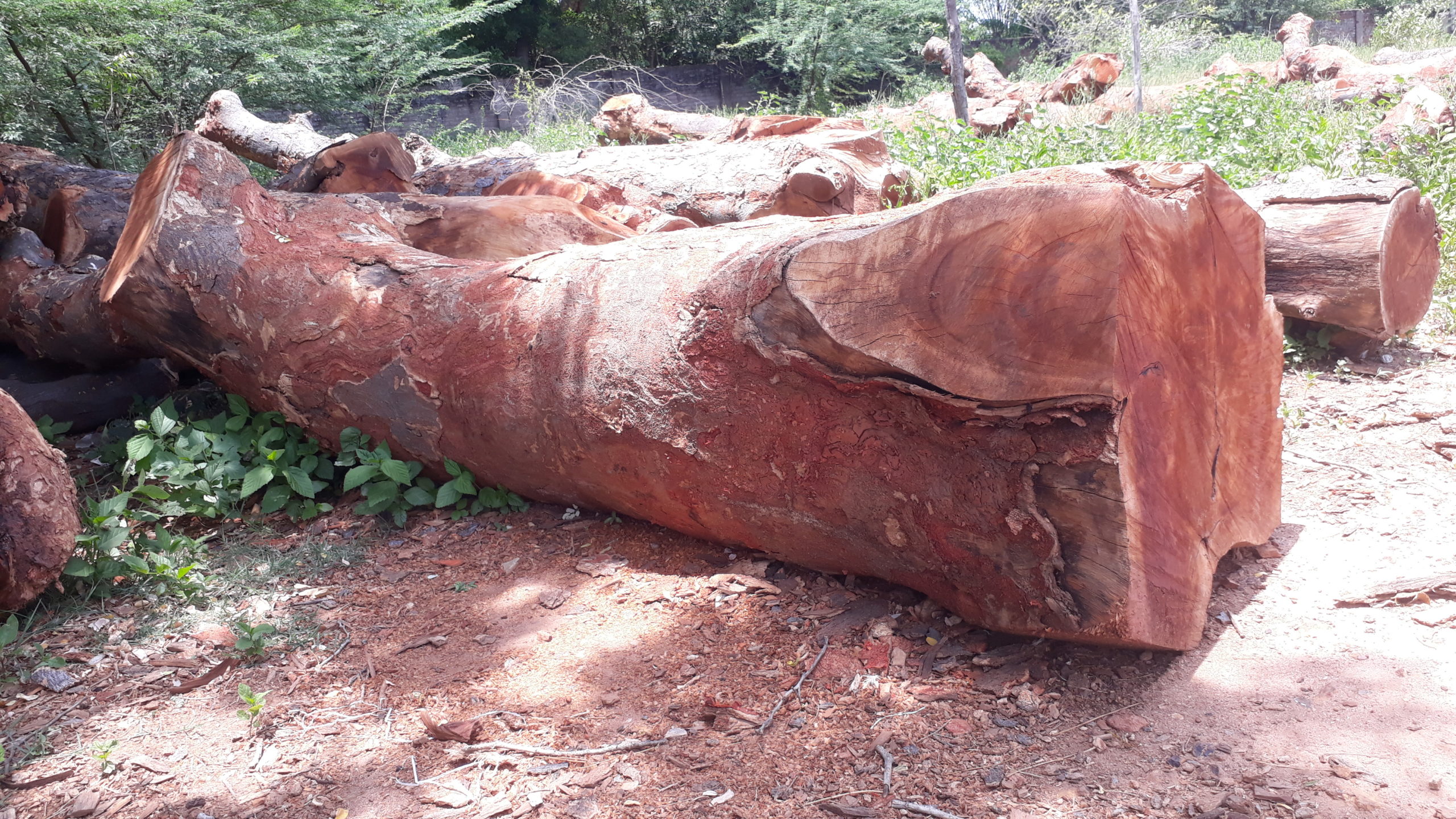
Figure 2. Jackfruit tree, drying. Credit: Author image.
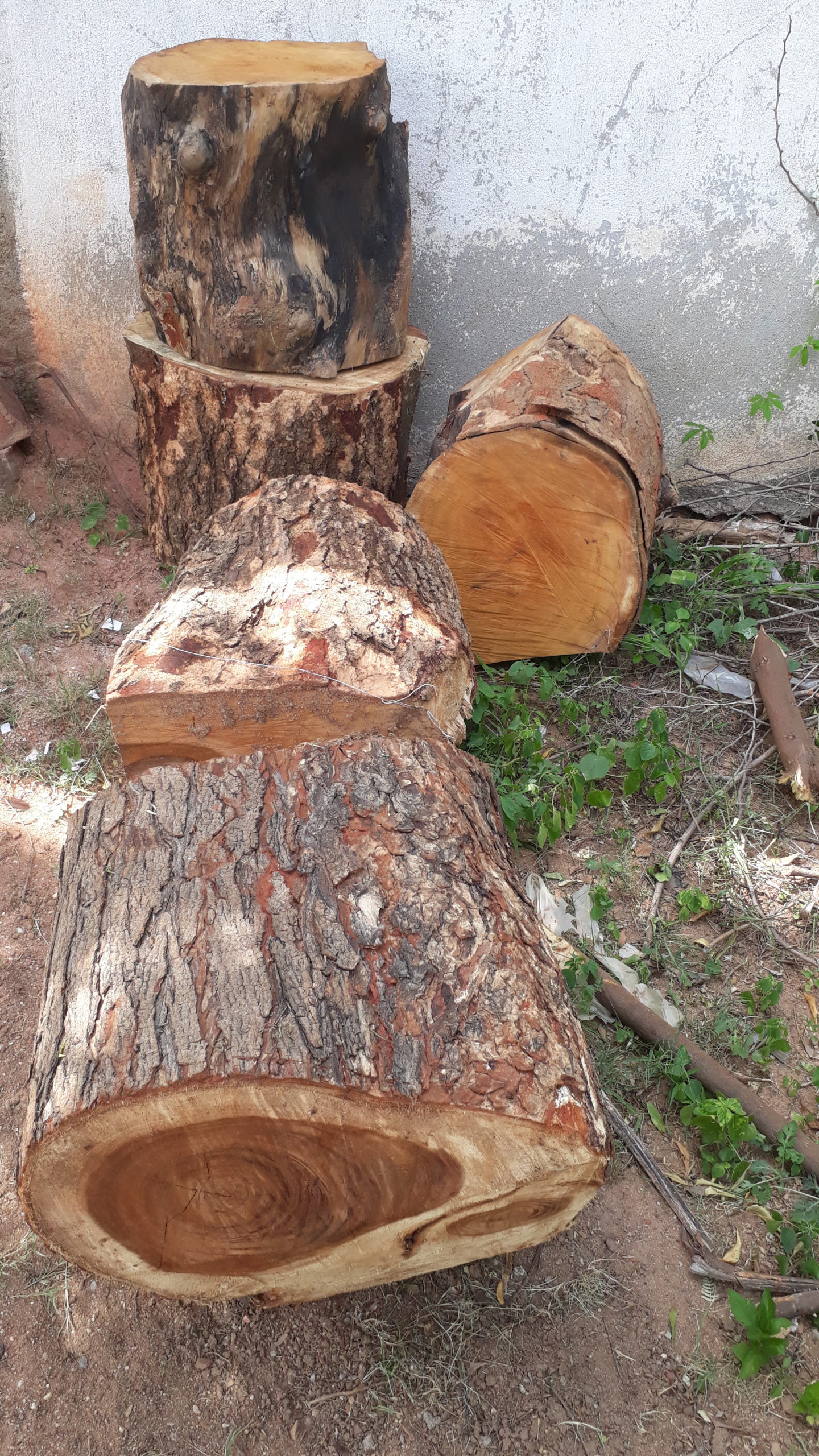
Figure 3. Jackfruit tree cut to usable size. Credit: Author image.
Panruti wood instruments are sent to music stores across the state of Tamil Nadu. Even in places like the Western Ghats, which have an abundance of jackfruit plantations, musicians request instruments made from Panruti wood.[9] The craftsmanship of Panruti is known among the music world beyond Tamil Nadu is linked both to the fame of craftworkers, but also to the special qualities of the wood cultivated in Panruti’s plantations.
Crafting Sound part 2: Wood log and wedlock
The fame of Panruti’s instruments also rests on the skills of craftspeople, skills honed through their collaborations with musicians. The experiences of one craftsman, Anthony, offer some insight into the ways that the craft of instrument making is learned, practiced, and shared. He is an ITI (Industrial Training Institute) certified carpenter in furniture making, but he has never made any furniture. [10] He learned the craft of drum making as an apprentice of Ezhumalai, who in turn was one of the first apprentices of Somu Aasari. [11] Anthony has an independent workshop with apprentices of his own. Anthony’s main tool is a lathe that has been designed for turning metal but is now customized for making wooden drums (see figure 4.)
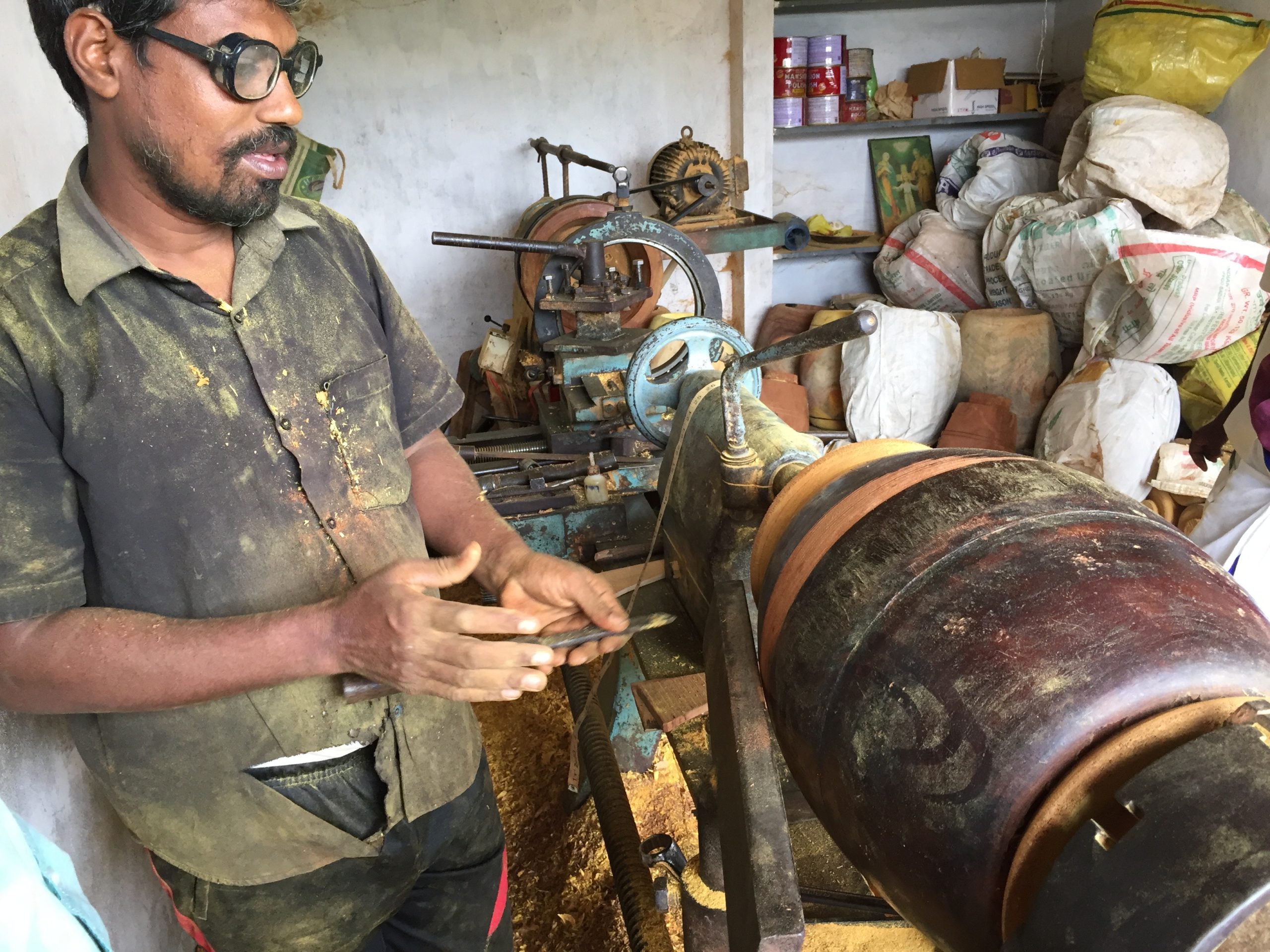
Figure 4. Thavil craftsman Anthony in his workshop. Credit: Photo by Roland Wittje.
He receives orders from musicians and music stores in South India, Malaysia, Singapore, and Sri Lanka. The technological knowledge of crafting musical instruments has circulated beyond caste and religious boundaries, as craftspeople like Anthony share the knowledge about the trade with peers and beginners alike. Anthony has an apprentice named Johnson who is studying for a Master’s Degree in visual communication at the local college while he comes to Anthony’s workshop to learn the craft of drum making.[12] Apprentices like Johnson learn the technical skills of handling the tools and crafting the instrument, as well as knowledge about choosing jackfruit wood. Apprentices, therefore, gain technical, experiential, and tacit knowledge of the craft trade in order to become independent and successful craftworkers like Anthony.[13]
One important dimension of this craftwork is working with local musicians. Choosing a wood log for her or his thavil is a special occasion for every budding thavil musician. The thavil teacher comes to the workshop of the instrument maker, with whom the teacher has a relationship of trust, to choose a wood log for their student’s thavil. The log is carefully chosen by the instrument maker and the teacher. The teacher then ritually touches and hands the log to the instrument maker to start work.[14] The process of crafting the instrument depends on the mutual trust between the teacher, the student, and the instrument maker. The sound that a musician’s instrument produces has real implications for a musician’s professional career, and this, in turn, depends on the jackfruit tree selected for the instrument. Raju, a thavil musician says that for a young musician the choice of log is a form of “wedlock” as the instrument will accompany that musician until their death. Raju points out that choosing the right wood log requires knowledge and experience on the part of musicians too.[15] Contemporary music schools do not teach student musicians how the instrument is crafted, even if instrument making is part of the syllabus, they usually skip it. Yet such knowledge can be vital.
Raju has a thavil which is more than four decades old. He acquired the knowledge of how to choose the wood from his teacher. He explains that the root of the tree should not be used for making a thavil, and there should be no suli (knot) in the wood; if the log contains a suli, the instrument body cannot bear the weight and it will soon crack[16] The tree should be at least thirty years old. Thavil musicians believe that if the tree has been exposed to natural sounds during its growth, it will produce a sound that will be sweeter to the ears. Therefore the tree should not have grown on the roadside where it has been exposed to unwanted noise.
To be sure the thavil meets these requirements, the musician must have a strong relationship of mutual respect and trust with the instrument builders. For reasons like this Thavil lecturer Dr. P. Shanmugam asserts that musicians will not change their instrument maker once they have established trust. [17] An instrument maker rewards this trust by carefully constructing the instrument according to their specifications. Craftsmen like Anthony have their own network of musicians who come to the workshop to get their instrument ready for performance and similarly, musicians wait (sometimes until midnight) during peak seasons to get access to their favored instrument-maker. (see figure 5).
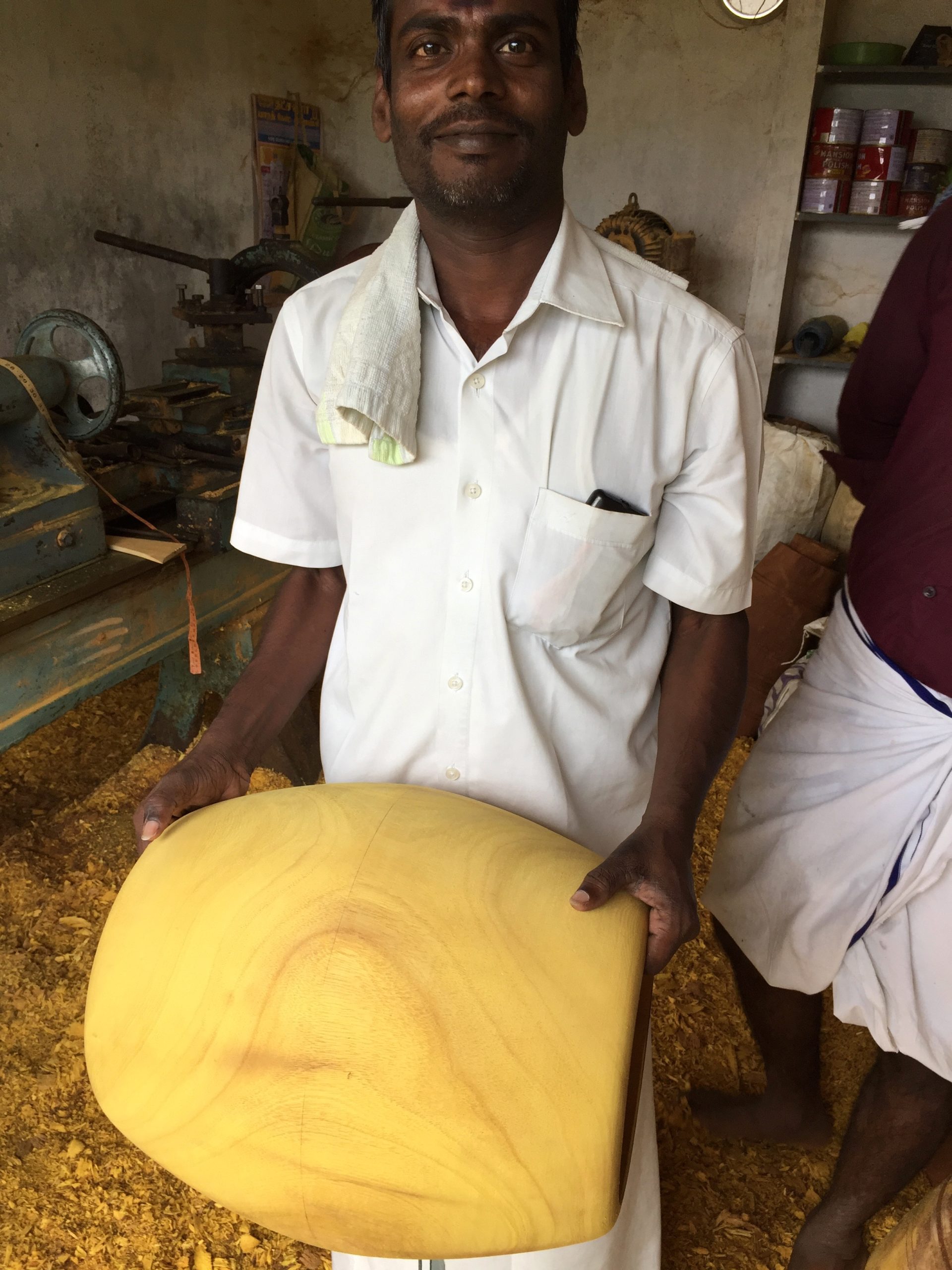
Figure 5. Thavil musician Murugan in Anthony’s workshop. Credit: Photo by Roland Wittje.
Conclusion
Panruti is the place where a community of musicians, planters, and craftsmen have established a common space where they exchange ideas and knowledge about music, instruments, and jackfruit wood.[18] Rather than thinking of artisanal knowledge as residing solely in the minds of artisans, the knowledge about wood and sound moves from the jackfruit tree to the craftsman who crafts the instrument to the musician who performs with the instrument for the public.
The feature image photo is courtesy Raju.
Copyright 2021 K. Thamarai Selvan.
K. Thamarai Selvan is a Ph.D. candidate from the Department of Humanities and Social Sciences, Indian Institute of Technology Madras (IIT Madras) India, specializing in the history of science, technology, craft, and education.
[1] Thavil is a percussion instrument. The body of the drum is made out of jackfruit wood (palaa maram).
[2] B.M. Sundarum, Thavil – Demonstration lecture 1983, p. 74-89.
[3] K. Natesa Aiyar, “Agriculture and Industries”, Varthakamithran, 1915, Vol 1 (1).
[4] Anthony, Interview notes, 11th August 2019.
[5] Anthony, Field interview 22 December 2018.
[6] Madras District Gazetteers.
[7] Arts and Industry Survey Report of Certain Districts of Madras Presidency 1885-1888.
[8] Anthony, interview notes, 11th August 2019.
[9] Field notes, Thirunelveli, February 2019.
[10] Anthony – Senior craftsman who runs an independent workshop and having more than twenty years of experience in instrument making.
[11] Ezhumalai – Senior craftsman who trained most of the craftsman in instrument making in the Panruti region.
[12] Johnson – A part-time apprentice works in Anthony’s workshop for the last two years.
[13] Johnson, Interview notes, 10th August 2019.
[14] Raju, Interview notes, 10th August 2019.
[15] Raju is an All India Radio ‘A’ grade Thavil musician having more than thirty years of experience.
[16] Suli – a ring-shaped (toroid) surface on the main trunk of the wood created by its branch.
[17] Dr. P. Shanmugam – Thavil lecturer, Puducherry, Interview notes, 15th August 2019
[18] J. Lave and E. Wenger, Situated Learning: Legitimate Peripheral Participation, New York: Cambridge University Press, 1991 and Jean Lave, Cognition in Practice: Mind, Mathematics, and Culture in Everyday Life. Cambridge, U.K.: Cambridge University Press, 1988.